NEWS & COLUMN お知らせ&コラム
再び注目度が高まる生産財としての3Dプリンタ、その種類や特徴とは?
様々な業界で現在注目されている3Dプリンター。CMなどでも度々耳にする機会が増えてきていますが、実際はどんなもので何ができるのかがイマイチよく分からないといったお声をよくいただきます。
こちらのコラムではそんな3Dプリンターの基本的な内容から、各造形方式や導入事例などを詳しくご紹介いたします。
3Dプリンターとは
3Dプリンターとは、3D CADなどのソフトウェアで作成され設計データ(STL)を元に断面形状を積層し、立体造形することができる機器のことを指します。
3Dプリンターは、液体樹脂に光を当てながら少しずつ硬化させる「光造形方式」や、一定の温度で熱溶解させた樹脂を積み重ねる「FDM方式」の他、粉末状の材料に高出力レーザーを照射し焼結させたりするものなど、さまざまな技法で材料を積層して立体物を成形していきます。
3Dプリンターの歴史
- 1980年
-
名古屋市工業研究所にて小玉秀男氏が世界で初めて光造形法を発明。
- 1983年
-
米)チャック・ハル氏がSTLフォーマットを発明。
- 1986年
-
同氏により3D Systems Corp設立、翌年「SLA1」として商品化。
「3Dリソグラフィー特許」を出願。 - 1990年
-
米)Stratasys社がFDM(熱溶解積層法)技術による積層装置を商品化。
FDM方式を特許出願。 - 2009年
-
FDM方式の特許が切れ、多くの3Dプリンターメーカーが参入し、低価格化が進む。
- 2012年
-
米)オバマ大統領が3Dプリンターを後押し。
同年、米)Wired元編集長のクリス・アンダーソン氏が『MAKERS』を出版。 - 2014年
-
レーザー焼結法の特許が切れ、金属積層造形にも複数の企業が参入。
3Dプリンターが対応している材料とその特性
様々な方式の3Dプリンターや対応している材料から、どのようなシステムを選んでいけば良いのかをご紹介いたします。過去に CAD/CAM システムを導入した方であれば経験済みだと思いますが、NC加工機に関しても対応している軸数やスピンドルの仕様、制御装置、さらには対応する CAM ソフトウェアによってさまざまな種類が存在し、検討に必要な知識をつけるのにそれなりの時間を要します。3Dプリンターはそれ以上に機種が多いですが、機種ごとの制約も多いという狭い範囲での選択が迫られるデジタル生産設備だと考えられます。3Dプリンターを論理的に理解するために、工業界で3Dプリンターを導入検討するユーザーがどのように3Dプリンターを選んでいるのかを参考にしながら整理していきたいと思います。 最初に考えるべきことは、その造形物をどのような目的で使うのか、そしてどの材料を適用するのか、であります。たとえば、デザインを確認するためなのか、使い勝手を評価するためなのか、機能性を評価するためなのか、治具や生産設備の部品としてなのか、最終製品としてなのかなど、まずは目的を考えます。この目的によって材料の特性が絞られてきます。その材料に求められるものは、たとえば耐熱性・耐久性・精度・色・透明度・柔軟性・消失性・劣化性・軽量性・耐水性・安全性・滑らかさなどがあります。
材料に求められる特性が決まってくると材料の種類が特定されます。常温では変形しにくいが熱を加えると軟化して成形しやすくなり、冷やすと再び固くなる性質をもった樹脂のことを熱可塑性樹脂といい、一般的な汎用プラスチックや ABS、PLA、エンプラ、ナイロンなどがそれにあたります。歯科業界でも導入が進んでおり、歯科用材料で使われるPMMA や PEEK などもこの熱可塑性樹脂です。その他には紫外線などの光エネルギーによって液状樹脂を個体に変化させる光硬化性樹脂も良く使われる材料で、エポキシ樹脂やアクリル系樹脂がベースとなっています。粘りが強く耐久性の高い樹脂や耐熱性が強化された樹脂、熱可塑性樹脂である ABS 樹脂と似た特性をもつ樹脂やポリウレタン系の弾力性のある樹脂なども開発されています。燃焼させて消失されるような鋳造用レジンにはこの光硬化性樹脂が多く使われています。金属やナイロン系などの粉末状態の材料にはレーザーやハロゲンランプによる熱源を与えて溶融して固める方式を取ることが多く、表面は比較的ざらつきやすくなります。粉末材料がサポートの代替をすることができるため、造形時にひずまない程度の重量であれば格子状や鎖状の複雑な形状を造形することが可能となります。
目的と材料が決まってくると、あとはユーザーが求める造形サイズと造形時間、表面精度、そして価格となると思います。工業界で導入検討する際のポイントは、上記のような項目から考えていくことが多いです。医療や建設など特定の業界においては目的も材料もある程度限定されるため、候補となる3Dプリンターの種類も工業界に比べるとはるかに少ないかもしれませんが、基本知識としてこのような目的別/材料特性別の情報をもつことで論理的に理解しやすくなると思います。
3Dプリンター導入検討のワークフロー
3D プリンターを導入する目的と材料に求められる特性
3Dプリンターの造形方式
この方式は熱可塑性樹脂をフィラメント状にした材料を用いて、半液状に溶かしながらノズルから押出成形していくことで造形していきます。ABS やポリカーボネートなどの実製品として使われている工業用樹脂素材を使って造形することができるところが大きな特徴です。FDM 方式用のフィラメントを専門的に開発している材料メーカーも出てきており、樹脂素材にカーボンなどの特殊材料を混合することで ABS 樹脂よりも強度があり、耐熱にも優れているパーツを造形することが可能となります。溶かした材料を下から順番に積み上げていくため、中空構造やアンダーカットとなる部分にはサポート材とよばれる補強モデルが必要となり、複数のヘッドを持つ3D プリンターも多く、製品部分とサポート部分との材料を分けて造形し、サポート部分のみ溶かして製品部分を取り出すことでサポート除去工数を効率化しているものもあります。熱可塑性樹脂がそのまま使えるという点がポイントで、射出成型部品とまったく同じ物性を得ることはできないが他方式に比べると比較的近い物性を得ることができるため、造形物の適用用途は多岐に渡ります。
FDM方式の説明図
熱可塑性樹脂をフィラメント状にした材料を用いて、ノズルヘッド(オレンジ部)の上部から供給される材料を半液状に溶かしながら押出成形していくことで下から造形していきます。
一般的な二次元のインクジェットプリンターと同じような機構で、インクジェットヘッドから噴射した樹脂を紫外線で固めて積層造形していく方式です。この方式には光硬化性樹脂を紫外線で固めて積層するマテリアルジェッティング(素材そのものを噴射して積層)と、粉末状のパウダーにバインダーとよばれる結合剤を噴射して固めるバインダージェッティング(バインダーを噴射して固める)の2種類があります。この方式の最大の特徴はインクのような微細な状態から物体を造形するため、表面が非常に滑らかになることです。さらに二次元プリンターと同様に CMYK(シアン、マゼンダ、イエロー、ブラック)の掛け合わせによってさまざまな色を表現できるようにフルカラーやマルチカラーの造形も可能です。アメリカの Stratasys 社や3DSystems 社が代表的なメーカーで、工業界だけでなく医療業界でも鋳造用パターンの造形やスプリント、サージカルガイドなどに活用されています。生産性にも優れ、高精度/高品質である反面、導入コストや運用コストが比較的高めで、造形装置自体も大きなものが多くプロフェッショナル向けハイエンドマシンに分類されます。その他、イスラエルのXJet 社はステンレス鋼などの金属素材をサブミクロンレベルのインク液状にして噴射/高温融合して造形する金属プリンターもリリースしています。またアメリカの HP 社はインクジェット方式の新たな機種として、日本でも大々的に Multi Jef Fusionというモデルをリリースし、注目を浴びています。同社は熱可塑性樹脂であるナイロンの粉末材料に結合剤を吹き付け、加熱することで一気に固める独自の方式を採用しており、今後もさらなる開発と発展が期待できる方式の1つであると考えられています。
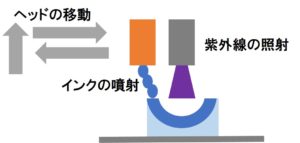
マテリアルジェッティングの説明図
インクジェットから噴射した樹脂を紫外線で固めて積層造形していきます。
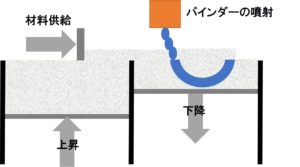
バインダージェッティングの説明図
粉末状のパウダーにバインダーと呼ばれる結合剤を噴射して固めていきます。
液体状の光硬化性樹脂に紫外線レーザーを当てて一層ずつ積層していく方式です。紫外線レーザーはガルバノスキャナと呼ばれるモーターとミラーを用いて、レーザー光をピンポイントで高精度に制御しています。基本的には造形エリアを走査もしくはハッチングのイメージで塗りつぶしながら照射していくため、形状の大きさや数、複雑さによって造形時間が異なってきます。今までは液体樹脂を入れたプールの上部からレーザーを当てて造形ステージを下げながら積層していく機種が主流でしたが、最近では Formlabs 社のようにトレーにカートリッジ式の液体樹脂を流し込みトレーの下から紫外線レーザーを当てて積層パーツを引き上げていく吊り下げ式も出てきています。この機構により小型化が実現し同社の「Form3」をベースに歯科向けにリリースした「Form3B」は歯科業界でも数多く導入されている代表的な3Dプリンタです。FDM 方式に比べると高精細で滑らかな表面を得ることができますが、造形後の洗浄処理や太陽光により硬化や変色もしやすく、また下で紹介している DLP 方式よりも表面の滑らかさは高いと言われていますが、一方で造形時間は多くかかることがあります。しかしながら Formlabs 社のように100万円以下の低価格と小型化を実現し、かつ生体親和性の高い光硬化性樹脂対応も出てきているため、医療に関係する部品や製品への活用も期待されています。
SLA方式の説明図
液体状の光硬化性樹脂に紫外線レーザーを当てて一層ずつ積層してきます。
光造形のカテゴリーに含まれ、SLA 方式と同様に紫外線で硬化する液体樹脂に LED 光線を当てて一層ずつ積層していく方式です。一度の照射で XY 方向の樹脂を露光して硬化させることができるため、SLA方式に比べて高速造形を実現しており、造形物の精度も高くバランスのとれた方式と言えます。プロジェクターによるデジタル画像の照射を行うためピクセルサイズが最小精度となり正方形の組み合わせとなるため、XY 方向の造形結果にピクセル模様が反映されることがあります。もちろん造形サイズを小さくしていけばピクセルサイズは細かくなり高精細な結果を得ることも可能です。造形パーツをどこに、どのように配置するかを考慮することが重要であり、生産スピードが求められる分野で導入が進んでいます。
DLP方式の説明図
SLA方式と同様に紫外線で硬化する液体樹脂にプロジェクター光を当てて一層ずつ積層してきます。一度の商社でXY方向の樹脂を露光して硬化させることができるため、SLA方式に比べて高速造形を実現しており、造形物の精度も高くバランスの取れた方式です。
SLS の特徴は金属でもナイロンでも従来の材料がもつ材質とほぼ同等に近い材料特性を実現することができる点にあります。つまり最終製品としての造形が可能となる積層方式の1つです。99.7% 以上の高密度を実現できるため造形物を研磨すると鏡面のような質感を得ることも可能です。代表的なメーカーはドイツの EOS 社やアメリカの3DSystems 社で、2014年に SLS に関わる特許が切れたため近年では低価格機などの普及モデルが続々とリリースされています。SLM 方式は欧州最大の研究機関であるドイツのフランフォーファ協会の研究所で開発された技術で、 SLS はレーザーで焼結するのに対し SLM はレーザーで溶融する方式です。代表的なメーカーはいずれもドイツですが、SLM Solutions 社や2016年にアメリカの GE に買収された ConceptLaser 社などがあります。造形に至る過程が若干違う程度で金属プリンターを使うユーザーにとってはそれほど大きな差異はないと言えます。いずれの装置も高出力レーザーを使用するため危険がともなうことと非常に高価になるため中小企業や市街地などのオフィス環境での運用はとても厳しいのが現実です。しかしながら最終製品が造形できるという利点もあり、SLS 関連特許が切れたことで今後はさらなる低価格化/小型化が進むと期待されています。
SLS / SLM方式の説明図
金属やナイロンの粉末材料にレーザーを当てて焼結させて造形する方法がSLS(レーザー焼結法)、レーザーを当てて溶融して造形する方法がSLM(レーザー溶融法)となります。
LINE UP
データ・デザインにて取り扱いをしている3Dプリンターメーカーをご紹介いたします。
カーボンと金属に対応した生産設備強度/耐熱性を備えた生産現場向け3Dプリンタ
「Markforged(マークフォージド)社製3Dプリンタ」はFFF方式をベースに特殊材料に特化したとてもユニークな3Dプリンタです。カーボンファイバーを利用したコンポジット積層やMIM(金属粉末射出成型法)とAM技術を融合した新しい金属積層方式により最終部品のオンデマンド生産を推進します。
プロトタイピングからプロダクションまでこの1台で設計/製造現場のニーズを実現
「Formlabs社製3Dプリンタ:Form3/Form3L」は、最新造形方式「Low Force Stereolithography|LFS」を採用し、高精度/高品質な3Dプリンティングを実現した業界最高レベルの3Dプリンタです。
導入事例
Markforged社製3Dプリンタを活用し、コスト削減や開発期間短縮に成功した事例をご紹介いたします。