CASESTUDY 導入事例
工業デザイン&製造
3Dプリンティングによる自動車部品製造プロセスの最適化
Dorman Products 社
2022.06.06 更新
コンピューターチップの不足、出荷の遅れ、工場の操業停止などが原因により、過去2年間で新車・中古車ともに価格が高騰しています。現在、所有している車の保証が切れた後、新車やトラックを購入できないことが多いため、車を長く走らせるためのメンテナンスや定期点検がますます重要になっています。自動車メーカーは部品を販売し、ディーラーでサービスを提供していますが、彼らも同じようにサプライチェーンに問題があるため、一般ドライバーにとって手頃な価格ではありません。
Dorman Products社は、100年の歴史を持つ小型車と大型車の交換用自動車部品メーカーですが、生産スケジュールを短縮し、品質を向上させるために3Dプリントに注目しました。同社は、OEMが絶えず追加する新しいメーカーやモデルに対応するために、2つの拠点に計8台の3Dプリンタを活用しています。
Dormanのアディティブ・マニュファクチャリングリーダーであるChris Allebach氏と機械設計チームマネージャー、Eric Tryson氏は、Form 2、Form 3、Form 3Lステレオリソグラフィー(SLA)プリンタと複数のFDMプリンタを使用して、新しい製品の試作や、検証プロセス用のカスタム治具を迅速に作成するために活用しています。
「OEMでは、1つのパーツを設計するのに数人のチームを編成し、時には新車発売の2年前から設計を開始することもあります。私たちは、代替品の信頼性を確保しながら、迅速に市場に投入する方法を見つけなければなりません。3Dプリンティングによって、その場で試行錯誤し、変更することができるため、過去にはやらなかったようなプロジェクトにも門戸を開くことができました。高品質の部品になることが分かっているので、自分たちがやっていることに自信が持てます。」とAllebach氏は言います。
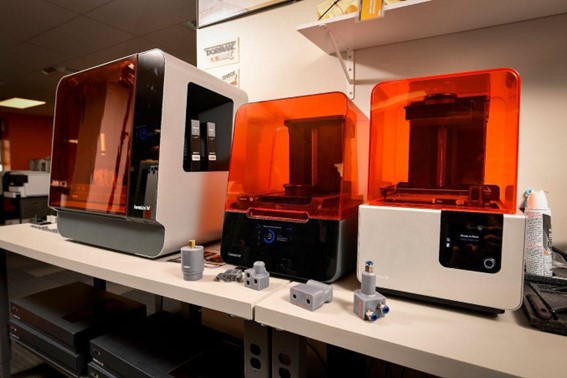
Dormanのエンジニアは、Form 2、Form 3+、Form 3Lのプリンタを使用しています。
10万種類以上の製品を作成
Dormanのエンジニアは、Form 2、Form 3+、Form 3Lのプリンタを使用しています。
Dormanが提供する製品の幅は驚くほど広く、数百種類の車種に対応する11万8000点(2021年12月25日現在)の部品を設計・データベース管理しています。「車に搭載されるものの大部分をカバーする幅広い製品を取り扱っており、毎年4000~5000点の部品を新たにリリースしています。」とTryson氏は言います。
Dormanが取り扱う製品は、キーフォブや基本的なエンジン部品から、複雑な電子モジュールや大型トラック部品に至るまで、多岐にわたります。 DormanはOEM部品の不具合を分析し、リバースエンジニアリングを行い、場合によっては設計を完全に見直して改善することもあります。また、車両システム全体を理解し、改良された設計を検証するために、オリジナルの部品を探しに出かけたり、時には車両を丸ごと購入したりすることもあります。
設計のプロセスでは、まず設計を変更できるようにデジタルで再現することが必要です。その後、部品はDormanの計測ラボに送られ、非接触レーザースキャンまたは高精度接触プローブが使用されます。ベンチマークデータはAllebach氏とTryson氏のチームに送られ、Solidworksを使ってパーツのリバースエンジニアリングが行われます。
「設計者が形状や寸法を再確認するために簡単なプロトタイプを作成し、その後、別の3Dプロトタイプを作成して、製品エンジニアに送り、レビューしてもらうのです。エンジニアは、実際に部品を手に取り、目で見て、自動車の部品と組み合わせて、適合していることを確認したいのです。」と、Trysonは言います。
しかし、Allebach氏とTryson氏の部署は、単に部品を交換しようとしているわけではありません。DormanのOE FIX™ラインの場合、元の設計を改善することも試みています。「私たちは単なるリバースエンジニアリングではなく、なぜその部品が故障したのかを分析し、判断し、どうすればより良くできるかを考えています。それは、材料の変更かもしれないし、一般的な設計の変更かもしれません。このような再設計を行う場合は、試作を行い、機能テストを行いたいと考えています。」とTryson氏は言います。
OE FIX™ パーツのプロトタイピング
再設計の一例として、多くのカーオーナーが故障していたエンジン部品があります。この部品はもともとプラスチック製で、エンジンが発する熱にさらされ続けると割れてしまうのです。Dormanチームは、この部品を分析し、計測チームによってスキャンし、アルミニウム鋳造で再設計しました。異なる材料で製品を設計することは、単に1対1の材料変更ではなく、部品がダイカストに適している必要がありました。設計変更後も部品の性能を維持するために、大規模な試作を行い、その都度テストを行う必要がありました。
「このような設計の繰り返しを数時間で、そして1日に2回できるようになったことは、とても助かります。3Dプリントする前は、最初からうまくいくことを願っていました。そうでない場合は、正しい部品を再注文するために数週間または数ヶ月を無駄にし、最初の部品を入手した後、再度微調整して送り返さなければなりませんでした。」とTryson氏は言います。
社内で設計したものを試作した後、Dormanは機能テストを行い、部品が同じように機能することを確認します。
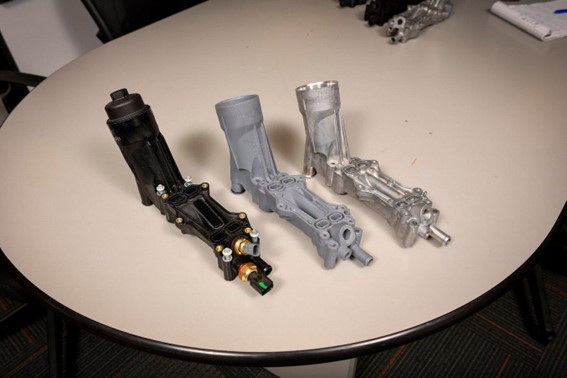
繰り返しテストしたエンジン部品
検証プロセス
製品ごとに機能が異なるため、試験プロトコルや検証プロセスもそれぞれ独自になります。2つの異なるパーツの検証プロセスで流体試験を行う場合、それぞれの形状が異なるため、パーツを固定するための異なる治具が必要になります。
-Chris Allebach
3Dプリンタをワークフローに組み込む前は、このカスタム治具が迅速な開発の障害になっていました。Dormanのように、毎年新しいモデルを生産するOEMに追いつく必要がある企業にとって、スピードが落ちることは新製品の機会を失うことになりかねません。
製品ごとに異なる治具のため、大量に注文することはできず、費用対効果の高い射出成形はできません。機械加工で作るしかないが、コストも時間もかかります。設計が完璧であることを確認した後、パーツを送り出し、何週間も待ってからパーツの検証を行わなければならなかったです。
「治具やゲージの場合は、機械加工工場に依頼しなければならず、5〜6週間かかります。コスト面でも、1つのパーツにつき5倍から10倍かかり、形状も従来の製造技術では限界がありました。3Dプリンタでは、製品の試作と同時にテスト用治具やゲージを開発し、最終的なデザインが決まった時点で、それをテストするための治具も用意できるようになりました。」とAllebach氏は言います。
ある検証プロセスでは、加圧ホース試験用に2つの3Dプリント試験治具が必要でした。1つは、ホースの一端を締め上げ、流体を流し加圧の限界を探るための治具です。もう1つは、実際の車のボンネットの下にある大きなラジエータを模擬したものです。このラジエータの嵌合部分だけを3Dプリントすることで、テストチームの操作性が向上しました。また、製造の組み立てラインにパーツを送り、品質管理の追加工程として、ラインから出てくるパーツの検証テストも行えるようになったのです。
「もし、相手方の部品が巨大なラジエータであった場合、それを何個も買ってきて、ほんの一部だけ切り取って出荷するようなことはしないでしょう。この方法では、欲しいものを作って大量に作り、それを流通させるだけです。結局、1個壊れても2〜3ドルだし、また造形すればいいんです。」とTryson氏は言います。
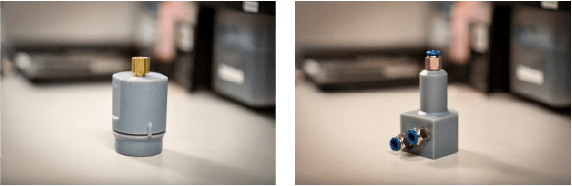
加圧ホース試験用の2つの固定具のうちの1つ。
また、この冶具をカスタマイズすることで、ラジエータ全体の形状をシミュレーションすることができ、固定具のためにラジエータ全体を探す必要がなくなりました。
可/不可テストのための厳しい公差
これらの製品が店頭に並び、ユーザーの車に取り付けられる前に、Dormanのチームはこれらの部品がどの程度の寸法変動に耐えられるかを正確に知る必要があります。そこで、寸法分析を行って、部品が「可」か「不可」かを判断します。このため、場合によっては厳しい公差が必要になります。Tryson氏とAllebach氏は、Form 3+とForm 3Lのプリンタを導入する前は、3Dプリントしたゲージを使用することが可能かどうか確信が持てなかったそうです。
「私たちは、Formlabsのプリンタで公差を満たすことができるため、多くの「不可」ゲージを製造しています。ある部品で、可能だとは思っていなかったのですが、部品のチェックを開始しようとしたところ、エンジニアがやってきて、直径で+/-0.05mmの公差を達成する必要があると言ってきました。その結果、振れ幅0.025mmの直径で造形することができました。Form 3Lでこのような公差が得られるとは信じられませんでした。」
とAllebach氏は言います。
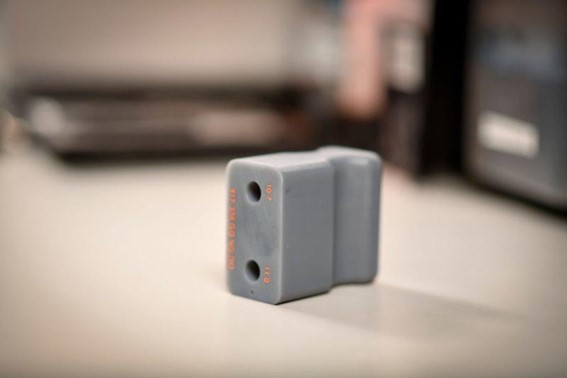
Grey Resinで造形された「不可」ゲージ
造形物の電気メッキ加工の仕上がり
Tryson氏とAllebach氏は、Dormanのマーケティングやセールスチームに送る前に、部品にちょっとした後処理をすることがあります。最終的に金属で量産する部品は、SLAプリントした部品を仕上げ加工してから、カスタマー対応部門に渡します。最近では、シャーシのチーム用にボールスタッドをGreyProResinで造形し、電気メッキを施してからマーケティング資料として同僚に渡しました(電気メッキはRepliform INCによる)。ただ一つ問題がありました。それは、表面の仕上がりが良すぎたことです。マーケティングチームは、「この部品は通常、鍛造や鋳造の後に亜鉛メッキが施されています。これを使えば、箱に入っている部品よりも見栄えがよくなる。」とAllebach氏は言います。
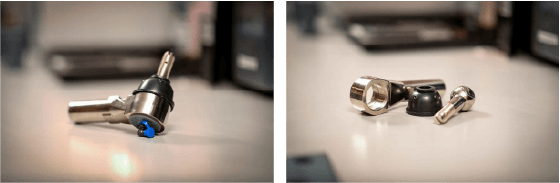
電気メッキを施したアセンブリ
Formlabsプリンタの費用対効果
Dormanが10年前に最初のFDMプリンタを入手して以来、Allebach氏とTryson氏は順調にプリンタを追加し、既存のユニットの容量を常に最大化し、Formlabs SLAプリンタの全材料ライブラリを活用しています。
Dormanの世界年間売上高は13億5000万ドル(2021年12月25日現在)に迫る勢いですが、それでも設備購入は正当な理由が必要です。「表面仕上げと寸法精度のためにForm 2を導入することにしましたが、私たちの場合、2ヶ月で元が取れることがわかりました。Formlabs製プリンタのコスト正当化やROIを検討する際、2年という時間枠ではなく、数ヶ月という単位で正当化することができるのです。このことは、3Dプリンタが価値のある投資であるという自信を私たち経営者に与えてくれます。」とTryson氏は述べています。
Tryson氏とAllebach氏は、この自信から、ちょうど1年前に最初の大型プリンタであるForm 3Lに投資することができたのです。他のプリンタと同様、1日10時間から12時間、時には夜通し稼働しています。材料ライブラリにあるすべてのレジンを使用しているため、大型部品と小型部品の機械的特性を一致させることができ、ワークフローがより効率的になりました。
-Eric Tryson
3Dプリンティングで未来を拓く
サプライチェーンの混乱はすぐに解消されそうもなく、自動車価格は新車・中古車ともに高止まりしています。電気自動車を製造するOEMが増えるにつれ、新型車の部品は軽量化され、新しい(多くの場合アディティブ)製造技術に最適化され、従来とは異なる材料で作られるようになってきています。自動車業界は、オリジナルデザインだけでなくアフターマーケットにおいても、アディティブマニュファクチャリング技術への依存を高めています。Dorman Productsはすでに現在の導入で先行していますが、Allebach氏とTryson氏はまだ前を見据えています。
「また、アンダーカットやリッジを追加しても、機械加工のようにコスト増加にはならないことを他の部署に教えています。思い通りの設計を完璧に再現する事ができるのです。」とAllebach氏は言います。
ROIが確立され、FDMやSLAの技術が身近になった今、チームは次にパウダーベッド方式を加える準備をしています。「より高機能な部品、より少量で機能的な部品となると、粉体造形に期待するところです。」とTryson氏は言います。