CASESTUDY 導入事例
工業デザイン&製造
産業用ロボットのカスタムグリッパーを3Dプリンタで製作
STS Technical Group 社
2022.02.07 更新
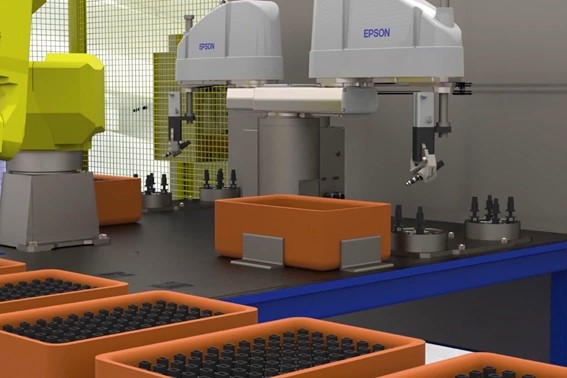
ウィスコンシン州に本社を置くSTS Technical Groupは、約40年にわたり、人材派遣、技術設計、エンジニアリングの分野でお客様とともに歩んできました。米国各地の人材紹介センターで250人以上の従業員を擁する同社は、日々変化する製造技術に対応しながら成長し、新しい革新的なサービスを提供しています。
STSがFormlabsの3Dプリント技術を利用する理由は、製造環境での広範囲な使用に適した様々な材料、医療用の3Dプリント部品の製造能力、高品質なプリント部品にあります。
この事例では、STSのエンジニアリングサービス担当ディレクター Benjamin Heard氏が、製造環境におけるフューエルインジェクション用のカスタムグリッパーの開発について説明し、部品を3Dプリントするメリットと鋳造や機械加工といった従来の製造方法との違いに焦点を当てます。また、3Dプリントされたカスタムグリッパーの機能が、従来から製造されているグリッパーよりもはるかに優れている理由も説明します。
特定部品の製造工程をどう選ぶか
特定の部品を製造するためには、鋳造、加工、機械加工、FDM(Fused Deposition Modeling)やSLA(Stereolithography)造形などの3Dプリンティングなど、多くの製造プロセスを開発時に考慮する必要があります。
3Dプリンタによる部品製造のメリットをいくつかご紹介します。
- 鋳造、加工、機械加工に比べ、高精細なデザインに対応可能。
- 鋳造、加工、機械加工に比べ、リードタイム、生産時間が大幅に短縮。
- 造形後の加工が不要なため、熟練工や面倒な段取りを必要とする高価な加工設備が不要。
- 耐久性と軽量性に優れた素材を豊富にラインアップ。
- 設計データがあればすぐに造形が可能であるため、在庫が不要。
- 3Dプリントは、ネジ・ボルト穴や六角穴などの取り付けのための形状を盛り込むことで、より取り付けに適した設計にすることが可能。
- SLAで3Dプリントされた部品が激しい衝撃を受けた場合、破損するためすぐに交換が可能。一方、金属部品は公差外の曲がりが生じやすく、規格外の部品を作り続けてしまう恐れがある。
- 破損部品の交換コストの低減と交換部品のリードタイムの短縮を実現。
- 造形された部品は、塗装や希望するコーティングで覆うことができ、デザインレビューが可能。
- ・加工中に溶けたり、欠けたり、割れたりして、機械加工に適さない材料の代替になる。
- 軽量化、梱包材削減による輸送コストの低減
鋳造、加工、機械加工、3Dプリンティング等の製造方法を決定する場合、最初に部品の必要な耐久性を検討します。従来のプロセスで製造された金属部品は、より高い強度、耐久性、耐摩耗性を持ちますが、多くの部品は、特定のエンジニアリング材料を使用した3Dプリント部品で充分な耐久性があります。
また、温度や湿度、腐食性物質に耐えられるよう、作業環境も考慮して材料を選択する必要があります。大きな部品を3Dプリントするのは難しいかもしれませんが、Form3Lのような大型3Dプリンタであれば、より大型の造形要件に対応することができます。
フューエルインジェクション用カスタムグリッパーの設計と3Dプリンティング
産業用ロボットのグリッパーを設計する際には、様々な要件を考慮する必要があります。例えばピッキングされる部品とグリッパーの材質、グリップ力、ピッキングされる部品の形状、周囲のクリアランス、ロボットアームの動作位置の許容誤差などです。
グリッパーフィンガーの材質は、数千回から数百万回のサイクルの後でもアームが摩耗しないように、通常、ピック部品よりもかなり強く、硬いものが選択されます。一般的なグリッパーの材質は焼き入れ鋼ですが、これはピッキングする部品の表面が柔らかい場合、傷がついてしまうことがあります。仕上げがデリケートな場合は、グリッパーにコーティング等を追加します。さらに、部品に追加の機械加工を施すために部品を所定の位置に移動させる場合、グリップの接触不良によって部品の位置がずれたり、加工不良が発生したりする可能性があります。
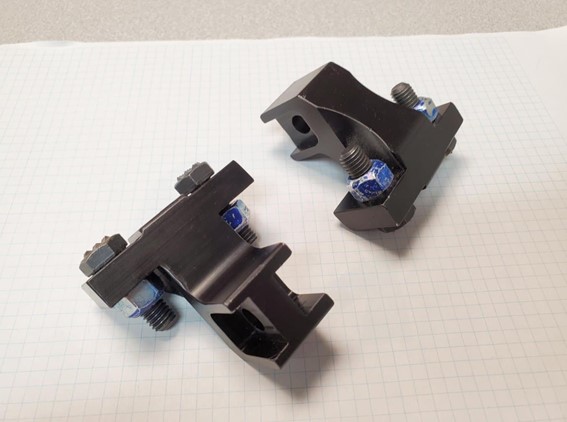
もともと空気圧シリンダーに搭載されていた汎用グリッパー
一般的に、グリッパーの爪は、円筒形や端が平らでないものをピッキングするために「V」字型にカットされています。この形状は、ピッキングされた部品に対して、片側あたり2箇所で信頼性の高い接触が可能です。さらに重要なのは、シンプルで費用対効果の高い設計であり、あらゆる工程にスケールアップできることです。
この設計の欠点は、力の集中がグリッパーと対象物の両方にストレスを与え、グリッパーが局所的に摩耗することです。さらに、「V」グリッパーは品物を抽象的にしか位置決めできないため、追加の製造工程のために二次的な位置決め機構が必要になってしまいます。
3Dプリンタで製作することで設計の選択肢が広がり、より大きな接触面積で力を分散できる、形状にフィットしたグリッパーを製作することが可能になりました。
この例では、Creaformレーザー3DスキャナーとVX Elementsモデリングソフトウェアを使用して、フューエルインジェクションの3Dスキャンを行い、グリッパーの設計をサポートしました。このスキャンにより、フューエルインジェクションのすべての隙間、シリンダー、開口部を丹念に測定し、詳細なデータを取得しました。このスキャンデータを3次元CADソフトに取り込み、ソフトの金型機能を使って非常に詳細なデザインを作成することができました。
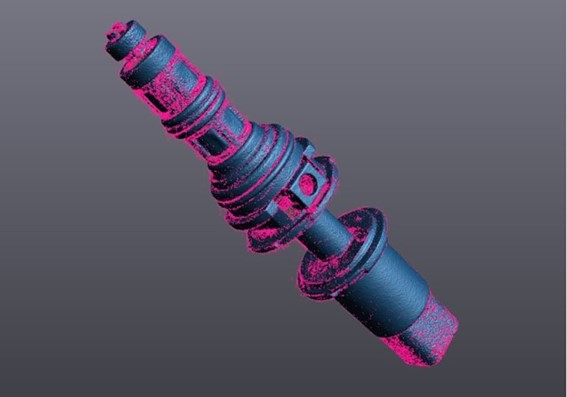
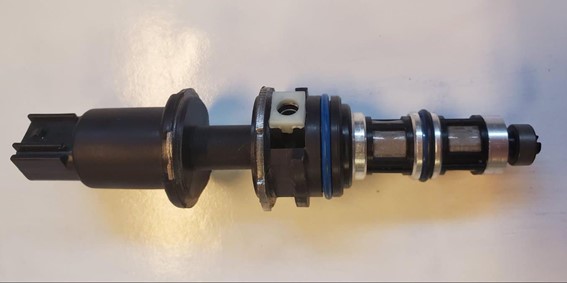
フューエルインジェクション(上)を3Dスキャンし、カスタムグリッパーの製作に使用するモデル(下)を作成
新しいデザインのラジアルグリッパーは、空気圧シリンダーのピストンに取り付けられた回転アームに装着するものです。
この新しいグリッパーは、FormlabsのForm3(SLA 3Dプリンタ)で試作・製造されました。Formlabsは、迅速なプロトタイプのためのDraft Resinなど、様々な材料を提供しています。今回はデザインの初期プロトタイプの開発にはBlack Resinが使用されました。一度の造形で、両方のグリッパーの半分をForm3にプリントすることができました。材料も簡単に変更できるため、最初のアイデアから最終製品にたどり着くまでの時間が短縮されました。
最終用途の部品を製造するには、生産環境を維持するために、より耐久性のある材料が必要でした。その結果、最終的なグリッパーの製造には、Rigid4000 Resinが使用されました。この非常に硬いガラス繊維入りポリマー素材は、高い耐久性と剛性を持ち、プリントパーツの仕上がりも魅力的です。
結果
不規則なグリッパーの設計と3Dプリントは成功し、期待通りに動作しています。3Dプリントされたグリッパーの性能は、以前のグリッパーをはるかにしのぐものです。
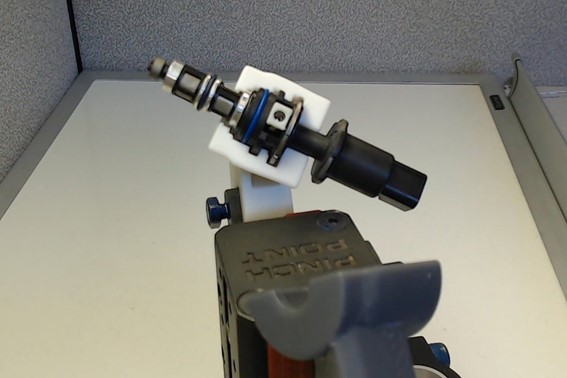
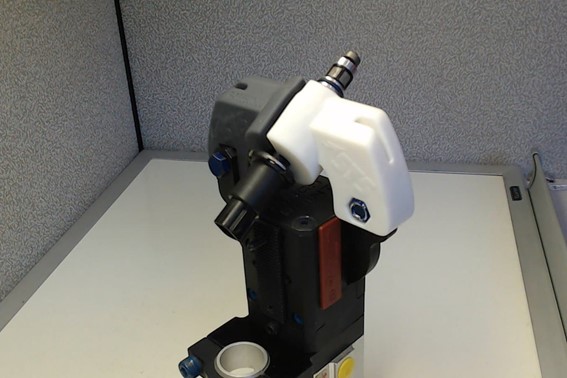
空気圧シリンダーのアセンブリ。3Dプリントされたグリッパーがフューエルインジェクションを支えている
3Dプリンタによるグリッパーのメリットは以下の通りです。
- フューエルインジェクションを掴む面積が広いため、フューエルインジェクションを傷つけたり、グリッパーを摩耗させたりする可能性のある、力の集中する部分が少なくなります。また、グリッパーが摩耗した場合でも、グリッパーを完全に包含する独自の設計により、グリッパーが問題ないレベルで作動することができます。
- グリッパーが放射状で動作するため、グリッパー内側の端のクリアランスを機械加工ではなく、設計に取り入れることができます。これにより、グリッピングキャビティ内の四角いエッジがなくなり、フューエルインジェクションにグリッピングし、完全に解放することが可能になります。
- 詳細なグリッパージョーにより、フューエルインジェクションの位置と向きが調整され、ピックした部品の向きを調整するための追加設備や製造ステーションが少なくて済みます。
- グリッパーを完全に包含する設計により、フューエルインジェクションを把持するために必要なグリッパーの圧力が下がり、材料処理装置に対する空気圧や油圧の要件が低くなりました。
- グリッパーは、樹脂の材料強度を最大限に高める独自の設計を行うとともに、六角ナットを包含する六角キャビティをアセンブリに含めることで取り付けを簡素化しています。
- SLA造形された部品のシリアルやラベリングは、造形工程で実現されるため、スタンピングやエッチングの工程は不要になります。
まとめ
Formlabs Form 3は、豊富な造形材料を備えており、生産用治具などのカスタム部品の製造において、従来の製造工程に代わる新しい選択肢になります。
造形部品は十分な耐久性を持ち、より詳細な設計のためにコストが大幅に削減され、わずかな時間で生産・実装することが可能です。これからの自動生産は、CADソフトで設計され、様々な材料で3Dプリントされた高精細な製品で構成されるようになることでしょう。
STS Technical Groupは、Formlabsの3DプリンタとCADソフトウェアを使用して、顧客のために非常に詳細かつ製品にフィットした部品の設計とエンジニアリングを行うことができます。