CASESTUDY 導入事例
工業デザイン&製造
どこでも炭酸水が飲める新たな水筒の試作品を3Dプリンタで作成
Spark To go 社
2022.03.28 更新
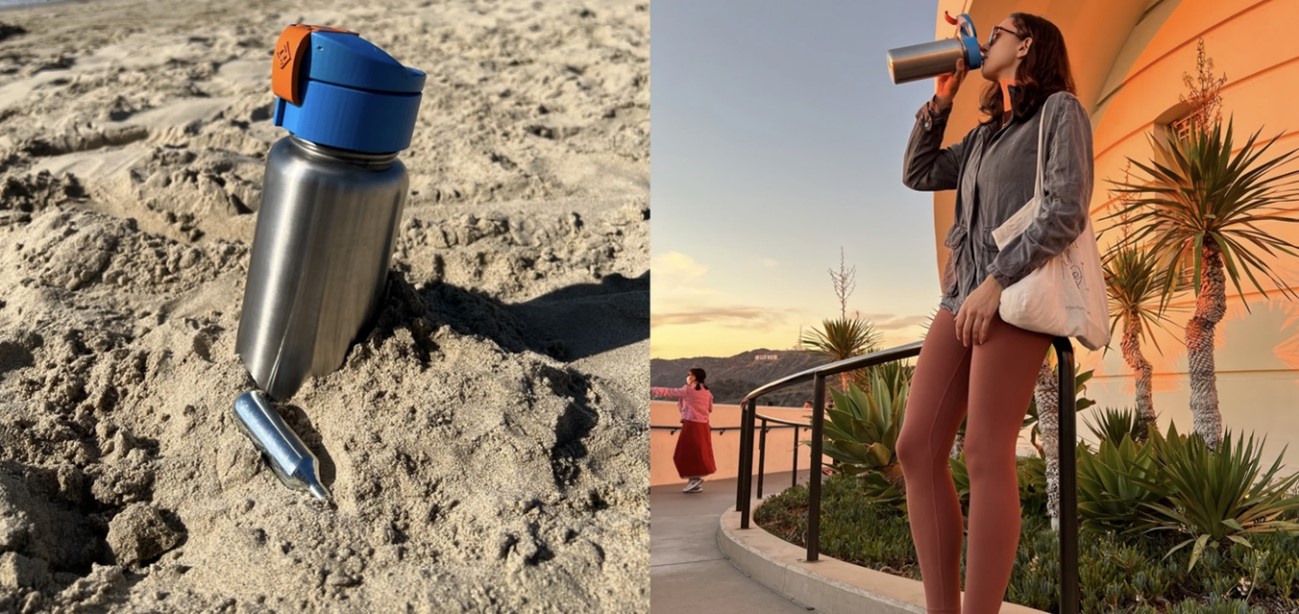
Spark To go社は、利便性と環境に配慮した新しい水筒のシステム構築に取り組んでいます。
ミュンヘンにあるスタートアップ企業の共同設立者2人は、普通の水筒に小型の炭酸システムを入れる事で、外出先で炭酸水を作れるというアイデアを思いつきました。
このアイデアを製品化するためには、複雑な構造、細かな部分、高圧に耐える高い強度を持つ試作品が必要でした。彼らはForm 3 SLAプリンタを用意し、コストと時間を効果的に使って、複雑なアイデアのプロトタイプを作る方法を発見しました。
Spark To Go社の創設者の一人であるPieter Prinsloo氏に、ペットボトル容器の炭酸水に代わるサステナブルな飲料水を提供するというミッションを、共同創設者のLuke Patruno氏とどのように追求しているのかを伺いました。
Spark To Go社がForm 3ステレオリソグラフィー(SLA)プリンタを活用し、コンセプトから最終プロトタイプまで、わずか2日で完成させ、スケジュールとプロトタイプ作成コストを大幅に削減した事例をご覧ください
ムダではない泡をつくる
「ドイツの消費者は、2020年に100億リットル以上の炭酸水を飲んでいます。これはアメリカが飲んだ量の9倍に相当する(人口はアメリカと比べると3分の1)。だから、ドイツは本当にスパークリングウォーターにとって特別な場所なのです。」とPrinsloo氏は語った。
しかし、ペットボトル飲料水業界は、使い捨てのプラスチックを大量に使用し、環境を著しく汚染しています。そこで、現在は家庭用の炭酸ガス発生装置が注目されています。水道水を数秒で炭酸水に変えることができるこのシステムは、世界中で人気が高まっています。
パトルノは、MBA(経営学修士)時代に「世界にポジティブなインパクトを与える製品イノベーション」というプロジェクトの一環として、持ち帰り用のミニ炭酸システムのアイデアを思いつきました。ガス圧で動く小型の炭酸ガス(CO2)カートリッジをボトルに装着し、ボタンを押すだけで水中にCO2を注入できるというものです。これなら、ペットボトルを買い直すことなく、外出先でも炭酸水を飲むことができます。
「どこにいても、普通の水道水を入れるだけで、炭酸が抜けて、いつも新鮮な泡のスパークリングウォーターができるんです」とPatruno氏は言います。
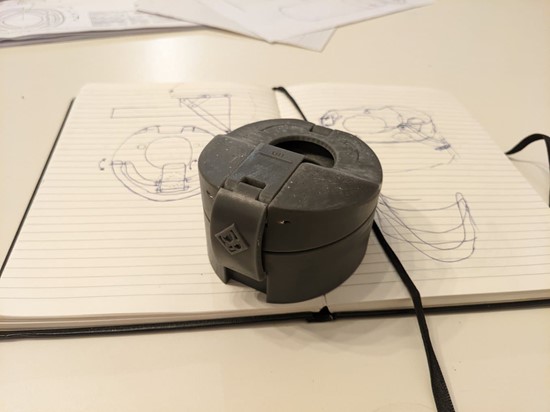
紙の上のラフスケッチから、Tough2000レジンを使用して3Dプリントされたキャップの初期デザイン
Luke氏とPieter氏は、2019年にミュンヘン工科大学主催の起業家イベントで出会いました。起業したいという共通の熱意と、手元にある革新的かつサステナブルなアイデアによって結びつき、2020年にPatruno氏のデザインに基づいた炭酸システムの製造を目標にSpark To Go社が設立されました。
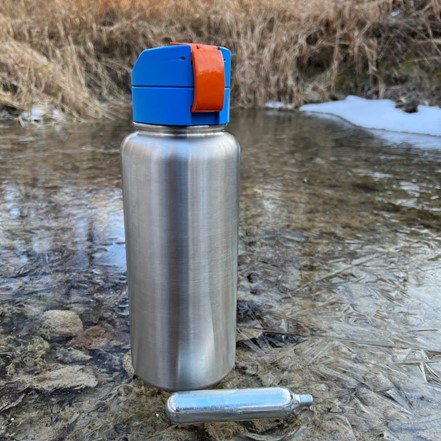
Spark To Goの試作水筒は、Form 3にTough2000レジンで蓋部分を造形し、その後に塗装を施しています。
正しい技術の選択
アイデアをコンピュータ上の2Dファイルから3Dプロトタイプにするために、Pieter氏とLuke氏はFormlabsのパートナーであるBeta2Shape社と連携して作業を進めました。
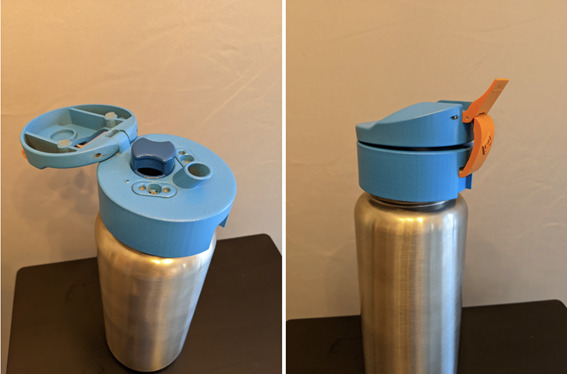
キャップと炭酸注入ボタンは、Form 3にTough2000レジンで試作した後、塗装を施しました。
小型炭酸システムのプロトタイプという特殊な技術要件を満たすために、様々な3Dプリント方式を比較検討しました。
「Beta2Shape社で短期間働いていたとき、3Dプリントや様々な技術について多くの知識を得ることができました。また、FDMとSLAを直接比較することもできました。」とPieter氏は語っています。
-Pieter Prinsloo
若い起業家たちは、機能部品の真のラピッドプロトタイピングを可能にするFormlabs SLAプリンタを選択し、製品開発段階を通してBeta2Shape社と密接に協力し続けました。3Dプリントの経験が浅い中小企業にとって、Beta2Shape社のサポートと専門的なアドバイスは、非常に役に立ちました。また、地元のショップで幅広い種類のレジンを直接比較し、自分たちの要求に関して評価することも可能でした。
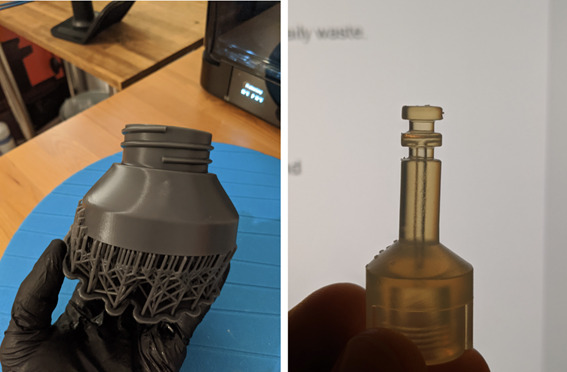
Tough 2000レジンを使って、ボトルの飲み口や炭酸の仕組みをプリントした試作品
Formlabsの材料ライブラリからいくつかの樹脂を試した結果、Tough 2000 レジンは圧力と温度の両方に耐えうる強度を持ち、かつ適切な寸法安定性と精度を備えていることが証明されました。
Beta2Shape社でのテストを基に、チームはForm3を購入し、炭酸システムとボトルデザインの開発を開始しました。
Form 3は、調整と後処理を100%コントロールしながら、非常に短期間でプロトタイプを作成することを可能にしました。
Form3によるラピッドプロトタイピング – 最高に働き者の社員たち
複雑な飲み口や炭酸化機構を自社で造形したことは、小さな会社にとって経済的に大きなメリットとなりました。ボトル全体を金属で製造するのは大きな投資になりますが、3Dプリントされた部品を使うことで、可能な限りコストを削減することができました。
-Pieter Prinsloo
24時間で2Dから3Dへ
投資家へのプレゼンテーションやアルファテストのための機能的なプロトタイプを作るために、Pieter氏とLuke氏はForm WashとForm Cureを含むFormlabsのエコシステム一式を購入しました。
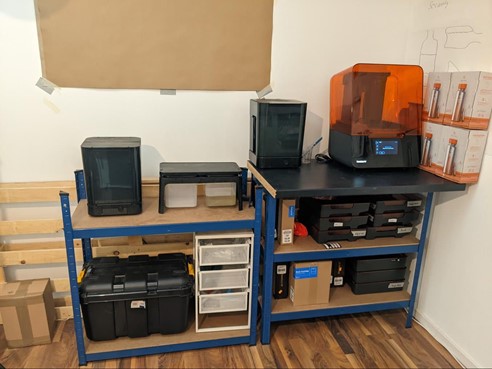
Spark To GoワークショップでForm 3、Form Wash、Form Cureでセットアップされたプリントファーム
「ボトルの上部をシステマチックにするために、100%3Dプリントした機能的なプロトタイプを用意しました。」とピエールは言います。
FormCureによる後処理により、Tough2000レジンの材料特性は最適なレベルに達し、曲げや衝撃、繰り返しの使用に耐える機能試作品としての引張強度や弾性率を持つようになったのです。
時間・コスト削減
「プロトタイプの製作時間を短縮し、12時間以内に新しいパーツを造形できるようになりましたが、まだ後処理が必要です。後処理を含めると大体48時間で、まったく新しいプロトタイプを作ることができるのです。」とピエールは言います。
Form 3によるラピッドプロトタイピングのスピードは、金属メーカーに試作を委託していた従来の方法とは対照的です。Spark To Go社のボトルをすべて金属で作ることを検討していたため、開発当初はこれを試しました。
彼らがすぐにFormlabsの3Dプリンタに仕事を任せるようになった決定的な理由は、2つあります。
時間:Spark To Goボトルのプロトタイプの場合、Form 3では48時間だったのに対し、外注では8週間もかかりました。14種類もの試作品があるため、外注では間に合いません。
費用:外注のプロトタイプ1つが、Form 3プリンタ1台分の費用になったそうです。
3Dプリンティングで生産に挑む
Spark To Go社は、6本のプロトタイプによるアルファテストを経て、次のステップとしてクラウドファンディングを実施し、この革新的な製品を市場に投入する予定です。
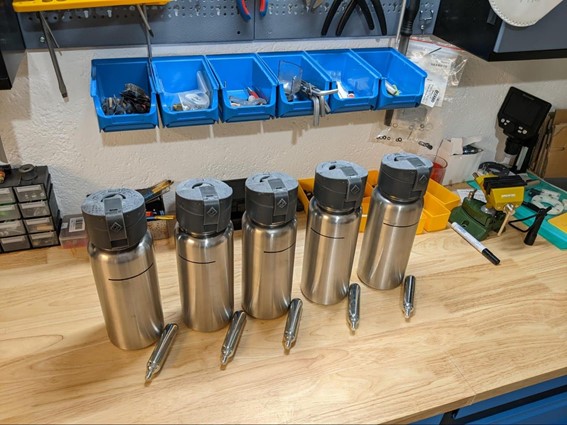
製品化前に外部ユーザーへαテストを実施したプロトタイプ5点
Formlabsのハードウェア、材料、ソフトウェアにより、Spark To Go社はトライアンドエラーを加速させ、プロトタイプのコストを大幅に削減しました。このような時間とコストの削減により、製品ラインを拡大し、より持続可能な未来に貢献する新しいソリューションや製品を生み出すことができるのです。
「私たちがこの会社を設立した理由は、ペットボトルの水に代わるものを提供することで、外出先でいつもペットボトルを購入する必要がなくなるからです。そして、この会社は、使い捨てプラスチックの他の分野にも発展できると考えています。」と、Pieter氏は今後の展望を語りました。
Pieter氏は、Spark to Go社のビジネス開発において、3Dプリンタが不可欠な存在になっていることを強調しました。
-Pieter Prinsloo