CASESTUDY 導入事例
Geomagic Control X工業デザイン&製造
3Dスキャンによる形状測定が検査工程を効率化!
さらにリバースエンジニアリング分野へも進出
株式会社浅野
2021.07.15 更新
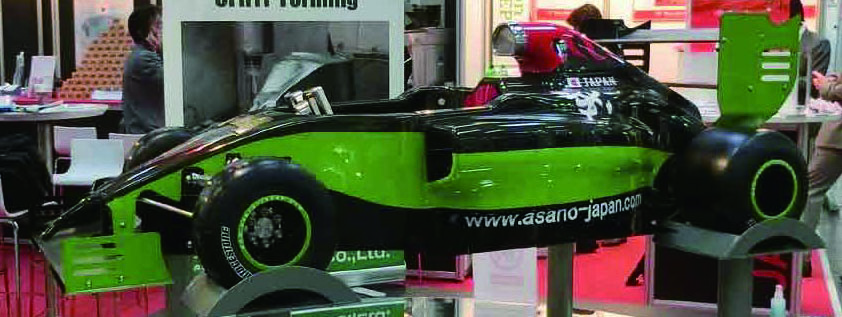
検査を2〜3倍スピードアップした形状測定技術
株式会社浅野は、自動車・二輪メーカーを中心とする各社の開発支援・生産準備支援事業を行う金属加工メーカーである。試作板金部品や量産用プレス金型、樹脂射出成形金型等の製造開発を展開。多彩かつ高度な技術基盤と共に、先端技術への積極的な取組みで知られている。
経営推進室の岸室長は語る。
「たとえば自動車分野で急速に拡大している軽量化ニーズに応え、CFRTP(熱可塑性炭素繊維強化プラスチック)による共同開発に取り組んでいます。ニーズを先取りして、何事にもまず挑戦する。そんなスタンスが当社の特長の1つなのです。」こうしたチャレンジングな風土は、各製造部門だけでなく同社の品質保証部門にまで共通している。
群馬工場で品質保証課の課長を務める今井氏は語る。
「板金部品の試作品作りを主力とする群馬工場の品質保証課では、いかにトライ枚数を減らし、一発で型を追い込めるかを課題としています。そのために、さまざまな新技術の導入・活用も積極的に進めています。」そんな品質保証課における取組みの一つが、従来の検査に替わる、より早くより精度の高い新しい検査手法の確立だ。その背景には、長年試作品検査の課題となっていた形状測定の問題があった。
「試作作りにあたっては全体の形状やサーフェスを把握することが重要になりますが、以前はそのための手段がなく、たとえばプレスした面スキ管理等にも検具が必要で、プレス直後は型合わせしか測定方法がありませんでした。そのため実際のズレ量も容易に把握できなかったのです。」品質保証課で検査を担当する松本氏はそう語る。当時、試作製作の現場では、実際のズレ量を具体的数値として把握する方法を求め、多くの手段が検討されていた。そして、その中で見出されたのがアーム型三次元測定器による形状測定だったのである。
「このアーム型三次元測定器を導入したのが2004年。業界でも早い方でしたね。そして、同時にこの機器との組み合わせで多くの実績を誇る形状検査ソフトウェアとして Geomagic Control を導入したことが、新たな形状測定の手法確立に繋がったのです。」(松本氏)
Geomagic Control は3D スキャナやアーム型三次元測定器によるインラインや繰返し検査工程を効率化する検査自動化プラットフォ ーム。多様な接触・非接触型計測機器に幅広く対応し、メリットを最大限引き出す。この Geomagic Control をアーム型三次元測定器と合わせて使うことで、よりスピーディで正確な試作品検査が実現されたのである。
「試作をプレスしレーザー測定して、その結果がNG だった場合、かつては形状の問題かレーザーの問題か判別が難しく、膨大な時間がかかっていました。しかし、導入後は、形状測定を行うことでひと目で原因を把握できるようになったのです。検査は以前の2~3倍までスピードアップし、大きく効率化を図ることができました。」( 松本氏)
無駄なハンドワークを省き測定作業を効率化
こうして導入された Geomagic Control とアーム型三次元測定器による形状測定は、PC 性能の向上と共に活用範囲を広げ検査手法を変えていった。
「製品素性の検査は3次元測定機や検具・治具を使っていましたが、それは量産品だけで、他はコストや時間の問題から検具を作れませんでした。」(松本氏)
そのため量産品以外は、3次元測定による穴位置の確認やサ ーフェスも任意のポイントを作って測定するしかなく、全体形状の把握は困難だった。フレーム系コンプ品の修正では、任意のポイントを作り穴位置を測定し、公差外の箇所をハンドワークで修正していたが、それが再び変化点を発生させて全体形状の把握を難しくする。結果、素性を明らかにすることに膨大な時間と労力が費やされていた。
「Control 導入後は順番が全く逆転しました。先にスキャニングして全体形状を把握し、その傾向を掴むことから始まる流れとなったんです。素早く形状を把握し傾向を掴むことで、修正方向をスピーディに決められるようになりました。」(松本氏)
その後ハンドワークで修正し、再度スキャニングして歪みを確認、という繰返しの後、全体的変化がないか確認して測定完了という流れが確立されたのだ。
リバースエンジニアリング分野への進出
「Geomagic Design X の導入は2008年頃。カメラ型非接触測定器の購入時に合わせて導入しました。実はあまり使われていなかったので、空いた時間に触るうちに面白くなったんですよ」と苦笑いするのはCAD. 機械加工統括Gr.のグループリーダー阿部氏だ。同氏はCAD、CAM、CAE等を駆使して機械加工を行うデジタルツールのエキスパートである。
「その頃話題だったリバースエンジニアリングに興味があって、いろいろ試していました。やがて社内でもプロジェクトが始まったので、そこでDesign X を使ったのです。」
それはラジコンボディのリバースエンジニアリングだった。既存のラジコンボディの形状をスキャニング。
Design X でデータ処理しフィーチャーベースのソリッドモデルを作り、金型を起して、プレスした金属で同じ形状のラジコンモデルを作りあげたのである。こうして徐々に蓄積されたノウハウが、リバースエンジニアリングという新分野の開拓に繋がっていったのである。
「あれから5〜6年ですが、すでに200点余のリバースエンジニアリングを行いました。特にアーム型三次元測定器と組み合わせて測定データの精度が向上してからは受注も大きく広がっています。」(阿部氏)
いまや同社のリバースエンジニアリングは新たな事業の柱へ成長している。
―― それを象徴する案件が、HONDA 車エンジンチューナー/パーツメーカー・株式会社スプーンの依頼による新製品開発だ。
これはHONDA「S660」フロント部のロアアーム左右とボディを一体化する新たな剛体プレート「STIFF PLATE FRONT」だ。S660のフロントはサブフレームのないモノコック構造だが、ロアアーム取付部の純正GUSSET PLATEの強度が足りず、ハードブレーキングやロール時に捩じれが生じていた。これを補填するため、純正パーツと同じプレス品でフロントのロアアーム左右とボディを一体化する、剛体プレートを製品化しようというのである。
「こうした製品は車体ベースで製作されるため、開発にも膨大な時間が必要でした。そこで Geomagic Control と Geomagic DesignX によるリバースエンジニアリングで取り組んだのです。」
そう語る松本氏がスキャニングでS660の車体下面のデータを採取し、Controlで処理。このデータを元に阿部氏が Design X でリバースエンジニアリングを進めていった。S660の現物をスキャンすることで精密なデータ化が可能となり、多角的な検証がスピーディに行えたのである。こうして完成した剛体プレートは、加工せずに簡単に取り付けでき、しかもアンダーカバーもそのまま装着できる精度を持っていた。そしてサブフレームのようにサスペンションとボディをワンボックス化することで、安定した操縦性を実現したのである。
「リバースエンジニアリングは、まだまだ大きな可能性を秘めています。近年は他のリバースエンジニアリングソフトも出ましたが、やはり全機能のバランスが取れ、莫大な点群も軽々扱える Design X がベストでしょう。Design X はフィーチャーベースのソリッドモデリングだけでなく、自動サーフェス作成などいろいろなモデリング手法を持っているので目的によって機能を使い分けています。試したいことはまだまだあるので積極的に挑戦していきたいですね。」(阿部氏)