CASESTUDY 導入事例
製造業研究
カーボンファイバー対応3Dプリンターの実力 (治具/試作 )
Caldwell-Manufacturing社
2021.05.19 更新
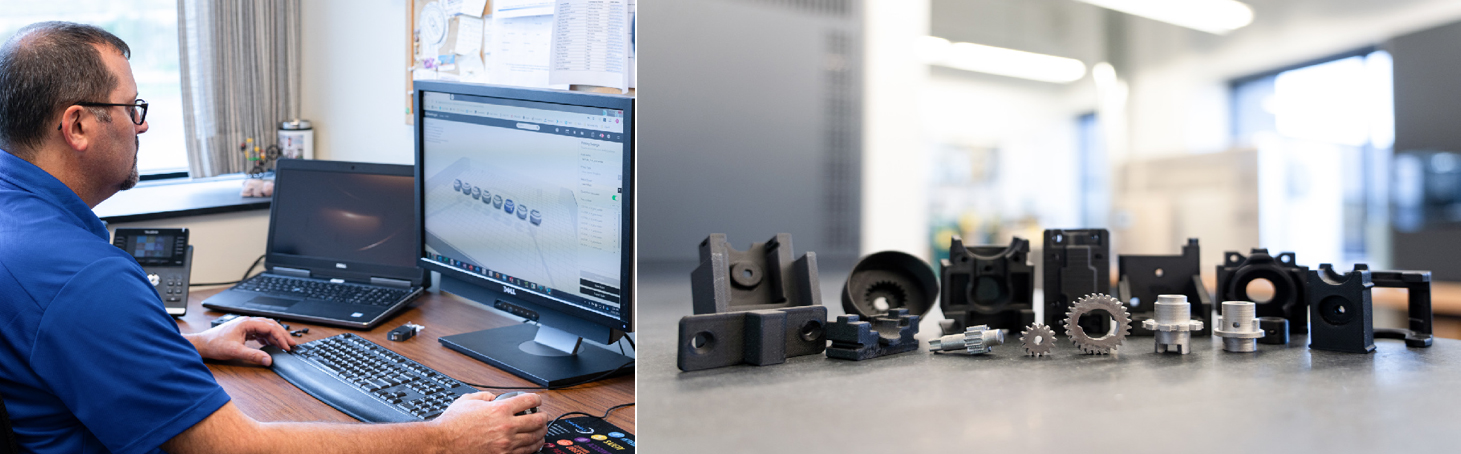
会社概要
Caldwell Manufacturing社は、ニューヨーク州北部に拠点を置く世界的に有名な窓・ドアの金具メーカです。Caldwell Munufacturing社の最高責任者である Eric Mertz は自身の会社の事を「統合されたサプライメーカ」と称し、ロックやラッチ、バネなど窓やドアを機能させるためのすべての部品を統合して製造研究しております。
こちらの会社は1888年に創業された老舗のメーカで、初期事業は今と変わらず窓やドアの製造メーカであり、1920年代には建設業界にも多角化しております。Caldwell社は現在、約70か国の国に販売をしており、アメリカ/イギリス/インド/メキシコに工場を備えております。
窓やドアの設計から最終製品まで統合して開発をしていると同時に、量産のための射出成型金型やバネも製造しております。
課題
ドアや窓などのハードウェア部品を製造するには治具や固定具、アセンブリ治具が必要でした。これらの治具/固定具はすべて社内で設計され、外注で鋼を素材として製作されていました。
設計と開発を合わせて約8週間ほどの工数を要し、一部の部品は海外から取り寄せる必要があった為、製品開発の総工数は6~12か月程かかっておりました。
治具や固定具などの単発的な製造でも外注もしくは、社内の加工工場に 依頼する必要があり、時間も費用もかかる為、このシステムを大幅に改善する必要がありました。
「結局、このような長いプロセスは組織的な業務になってしまう事もある。」とMertz氏は言います。従業員が仕事を辞めてしまう一つの理由として「繋がりを感じていない」からである。彼らは責任感を感じられず、仕事をするやる気をそがれてしまう。
2010年に開催された戦略計画の会議では 、どのような 技術が革新的なものになるかを検討し、3Dプリントが成功の鍵となるということで満場一致で合意しました。2014年、Caldwell社はFFF 方式の樹脂3Dプリンタを初めて導入しました。「3Dプリントは数年前から注目していた技術でした」とMertz氏は言います。当初、このプリンタは試作(RP)のために導入されましたが、3Dプリンタは形状やフィット感を評価するのに役立つだけで、機能的な評価をするのには役に立たないことが分かりました。
Caldwell社が必要としていた部品の多くは金属で作られており、部品の強度をテストする際にプラスチック製の3Dプリンタのフィラメントを使用するのは適切ではありませんでした。
Caldwell社の製品開発のマネージャーであるRick deNormand氏は次のように述べています。「私たちが本当に必要としていたのは、金属製の3Dプリンタを導入することでした。」
レーザーを使って積層するSLM方式の金属3Dプリンタは 、粉末の使用が面倒で取り扱いが難しく、導入するためのコストが高すぎるため、ニーズには合いませんでした。製品開発部は社内で簡単に運用できる手頃な価格のフィラメントベースの金属製3Dプリンタという「ソリューション」を探していました。
ソリューション
2017年、Caldwell社は他の3Dプリンタの検討を始めました。製品開発部のメンバーは製造業の展示会に参加し、Markforged社製3Dプリンタの説明を聞きました。3Dプリンタ業界最高のプリンタを製造しているMarkforged社の実績を聞いた後、彼らは金属3Dプリンタの Metal Xを導入することに決めました。「Markforged社の3Dプリントの歴史と、高い信頼性を確信し、Markforged社を導入する選択をしました。」とdeNormand氏は言います。Metal Xは、SUS630、インコネル、銅のプリントが可能な金属3Dプリンタです。
Caldwell社は、Metal Xと同時にMark Twoも購入しており、MarkTwoはカーボンファイバーなどの長繊維を連続してプリントする事で高強度な造形品を製作する事が可能です。製品開発部は当初、Metal Xは研究開発の用途で導入しましたが、その後、内製する為のツールとして使用するようになりました。Metal Xの導入により、Caldwell社のエンジニアや設計者は、従来、亜鉛やステンレスを使用して鋳造されていた金属部品の試作を造形する 事が出来るようになりました。「金属3Dプリンタのおかげで、これまで不可能だった部品の試作が可能になりました。」とdeNormand氏は言います。
従来の製造方法では、300ドル~5,000ドル程のコストであったものが、現在では30ドルとなり、製造にかかる日数も8週間から3日に短縮されています。彼らはMetal Xで造形した部品を試験し、顧客と試験結果を共有して評価を行い、フィードバックを収集して製品の設計に役立てることが出来るようになりました。「 設計サイクルをよりフェイルファストにする事が出来ました。」とMertz氏は言います。
「設計の方法、テストの方法、検証の方法についての考え方が大きく変わります。製品を生産する方法も変わります。すべてが変わりました。」
Caldwell社は、研究開発、テスト用のロボット部品、組立治具、工具、顧客のための後処理部品に至るまで、すべてのものに3Dプリントをうまく適用しています。現場で使用する治工具をMarkforgedで造形をし、治工具を使用する担当者は、改善のためのフィードバックや要望を出します。「担当者が変更すべき点があると感じたら、私はすぐに変更をします。」と製造エンジニアのPhillip Cole氏は言います。「設計変更を行い、それをプリンタに送信し、新しいものに交換します。以前は6~12ヶ月かかっていた作業が、Markforged社製3Dプリンタのおかげで6~12日で出来るようになりました。」
Markforged社製3Dプリンタを2台導入したことで、会社全体の堅苦しい組織的な環境が無くなり、自律性が増したとCEOのMertz氏は述べています。「これらのツールにより、従業員は自分の考えや要望を部品に落とし込むようになりました。3Dプリンタは我々の業務に欠かせないものとなっており、弊社の信頼度を向上させるものとなっています。」
今後の展望
Caldwell社は確かに業界を牽引していますが、まだ長い道のりがあると考えています。「この3Dプリントの技術が何をしようとしているのか、何に進化しようとしているのか、そしてそれが将来の少量生産をどのように変えるのかについては現状、氷山の一角に過ぎないと思います。」とMertz氏は言います。5年後には、各製造工場に少量、低稼働、カスタム生産部品用の3Dプリンタを導入する予定です。現在のところ、北米の4つの製造施設のうち2つの施設にMarkforgedプリンタを設置しており、約18台の少量 生産用の3Dプリンタを所有しています。これらのプリンタを使用して最終用途の部品の生産を開始しました。年末までには北米の残りの 2 つの拠点にもプリンタを増設する予定です。「私たちはこの3Dプリント技術のメリットを大きく実感しており、3Dプリンタの将来が非常に楽しみです。」とdeNormand氏は言います。
「Markforged社製3Dプリンタは、Caldwell社の研究開発部で最も使用されている機器となっています。治具/工具のブラッシュアップにより新製品や組み立てプロセスはより効率的なものとなっており、市場への導入をより迅速に行うことができます。」